Across the world, government, companies, and scientists are making efforts to develop sustainable energy sources and reduce our dependency on fossil fuels. Some of these new and renewable energy sources include solar energy, wind power, tidal energy, fuel cells and thermal energy just to name a few. The development of these energy sources has the ability to eliminate our need for fossil fuels that are harmful to the environment, provide us with more efficient methods for generating power and reduce power production costs. But there is another source of energy that many are throwing away every day. This energy source is waste heat. Waste heat common to nearly every type of production process, including energy, and can be harnessed for improving the efficiency of the systems we use day-to-day. Let’s examine how we can repurpose waste heat energy.
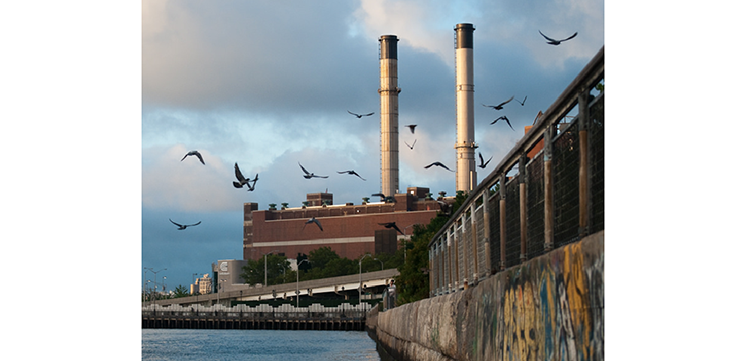
Con Edison, the CHP plant built by Thomas Edison in 1882
In principle, recycling heat is now a difficult process. In the US alone, it is estimated that as much as half of the energy produced is wasted and the majority of that is in the form of heat. In the 1880s, Thomas Edison built the first commercial power plant in New York and was able to channel the steam generated in the plant to neighboring buildings for them to use as a heat source. Edison’s power plant still exists today and plants like this are known as a cogeneration plant or a CHP (Combined Heat and Power) plant and are a common source of waste heat energy that can be utilized. Steel mills are also great sources of waste heat as they implement blast furnaces to produce steam that generates electricity and greatly reduce electricity costs and carbon emissions. This sort of waste heat is commonly generated by processes in machines such as thermal oxidizers, boilers, kilns, dryers, and steam system exhausts.
We also have the capacity to harness heat energy from other sources such as sewage sludge waste, fuel cell power generators and paper mills. Absorption chillers are also a valuable application for the utilization of waste heat energy. Sewage waste is collected and prepared in sewage digesters (fermentation) and then biological processes such as hydrolysis, acetogenesis, acidogenisis, and methanogenesis are implemented to produce biogas that can then be converted into electricity and useful heat through cogeneration of CHP. Fuel cells convert chemical energy to electricity and also produce water and heat. The heat from fuel cells can be recovered and utilized on site or at other sites in the immediate vicinity. Absorption chillers have an important role in waste heat recovery as the primary energy input is heat transfer. The washing and drying processes in paper manufacturing also provide waste heat energy that can be repurposed for heat in the manufacturing process or to generate electricity. Absorption chillers have an important role in waste heat recovery as the primary energy input is heat transfer. These and other application of waste heat recovery are slowly becoming common fixtures in plants around the world that realize the economic and environmental benefits of recycling an energy source that they have readily available.
However, there are still barriers to waste heat recovery technology development. Strategically, the fact that harnessed heat cannot be transported long distances limits the locations where waste heat can be utilized. Any site that will use the heat energy must be located in close proximity to the source itself. In most developed countries, it is illegal for a non-utility corporation to sell electricity directly to local companies that could use the excess energy. Also, while many governments provide subsidies and tax breaks for new and renewable energy sources such as solar and wind power, the subsidies provided for waste heat recovery are quite small in comparison. For example, in the US, companies can get as much as a 30% tax rebate for solar and wind power but only a 10% rebate is allowed for CHP.
As we can see, there are plenty of sources that provide us with waste heat energy that could be implemented to recoup costs, improve efficiency and reduce carbon emissions. LG is committed to extending these benefits to their partners from the design process to production and installation. The design of LG chiller systems allows them to take advantage of this energy source that is readily available at countless sites around the world. This capability makes LG chillers an excellent choice for their partners. As waste heat recovery technology continues to emerge, we will surely see the efficiency with which we use our energy improve greatly.